Bronze is an ancient alloy with a history of more than 5,000 years. In archaeology, the “Bronze Age” is even used to name the stages in the development of human civilization. Bronze is generally composed of 85% copper, 5% tin and 5% lead, and also contains elements such as zinc and nickel. The unique physical and chemical properties of this alloy make it an ideal material for statues.
The main components of bronze alloy are copper (Cu) and tin (Sn), usually the content of tin is between 5% and 30%, and different ratios of bronze alloy have different physical and chemical properties. Bronze alloys have good mechanical properties, corrosion resistance and wear resistance, as well as a unique luster.
According to Shanghai Nonferrous Metals Network, the bronze processing process mainly includes casting, forging, finishing and other steps. First is the casting process, the first step of bronze processing is to melt the copper and tin in a certain proportion of heat, and then poured into the mold for cooling and solidification, to get the desired shape. Finishing is the last process of bronze processing, which includes polishing, color plating, engraving and other steps. Polishing can make the surface of the bronze products smoother and increase the gloss; color plating can add color to the bronze products to make them more beautiful
History of Bronze Statues
Ancient Bronze Statues
The history of bronze statues can be traced back to Ancient Egypt during the Middle, New, and Late Kingdoms (1986-323 BCE), when a large number of bronze statues were produced using the lost-wax method for decorative and funerary purposes. In Mesopotamian art, the technique of bronze statue making also reached a high level, and may have been the first to produce high quality bronze statues at that time.
There were two main casting methods for ancient Chinese bronzes: the block-fan method and the lost-wax method. The predecessor of the original lost-wax method, the burned lost-wax method, has a very early origin, and the bronzes cast during the Spring and Autumn Period unearthed in Tongling are the masterpieces of the burned lost-wax method. Lost-wax method mainly includes making wax mold, making outer model, dewaxing, pouring and other steps. Bronze sculpture casting process before the Shang Dynasty are all muddy casting method, that is, a one-time casting molding. To the Shang Dynasty, the casting process is widely used, that is, the bronze sculpture body and accessories cast separately, and then combined together.
Ancient Greece’s bronze statue production method and China’s Bronze Age was widely used in the combination of pottery casting process is different, using the lost wax casting process. In Ancient Greece, the metal would be ground and polished, and then a varnish would be applied to the slightly yellow surface of the bronze to achieve the desired look.
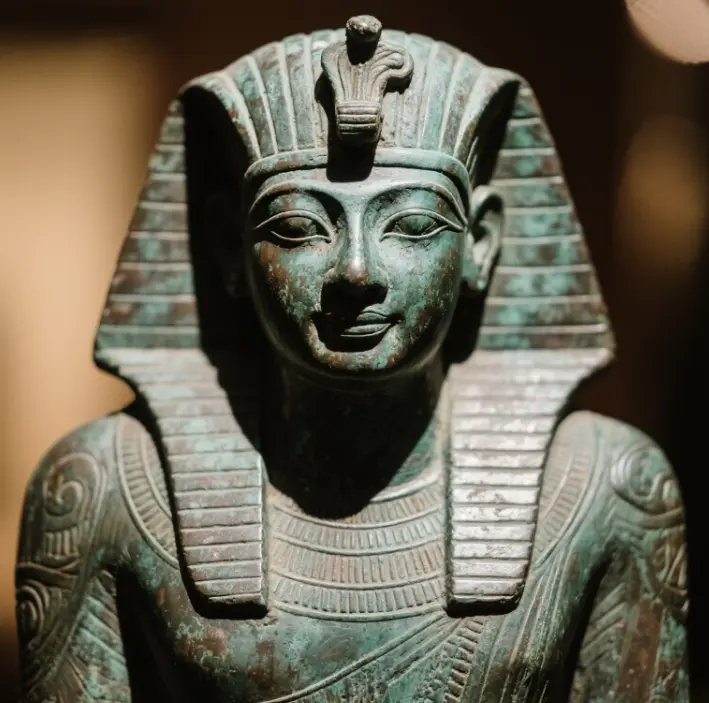
Modern Bronze Statues
Modern bronze statues inherit traditional bronze craftsmanship while incorporating modern artistic elements and techniques. Modern bronze statue making pays more attention to artistry and personalization, and sculptors express richer emotions and thoughts through the unique texture and color of the bronze material.
Modern bronze statue production is mainly divided into two methods: one is small or complex type, through the use of precision machinery casting, precision machining production by fine quartz sand layer, wax type good packaging, and then burned in the wax within the temperature of the net; the other is to improve the strength of the resin sand and fire resistance to adapt to the casting of large-scale bronze statue needs.
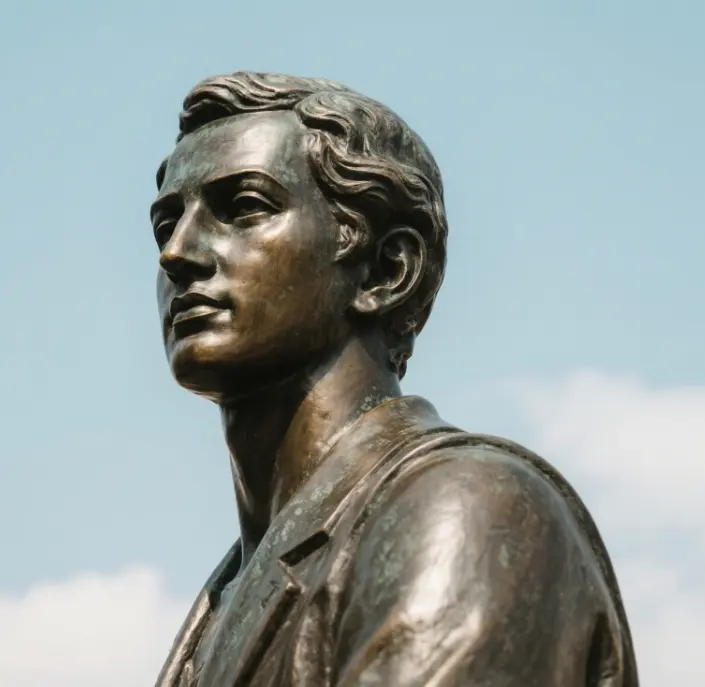
Bronze Statue Making Process
Traditional Making Methods
Lost Wax Method
The lost wax method is one of the main methods of bronze casting in ancient times, and is the ideal process for making complex shaped bronze statues. Lost wax method is divided into several steps, which are repeated many times during the whole production process because large sculptures often need to be cast in several parts – head, arms, hands, torso, etc.
The lost-wax method is made roughly as follows:
- First, the sculptor creates an equal-sized clay model of the statue.
- Then, a clay master mold is made around this model and split into several parts.
- After the master mold dries, wax is applied to the surface of the model in an even layer to form a wax mold.
- Next, a shell, usually made of clay or plaster, is made over the surface of the wax mold.
- When the shell is completely dry, heat is applied to melt the wax out, creating a cavity.
- Finally, molten bronze is poured into this cavity, cooled, removed, and polished and retouched to yield a bronze statue .
Bronze statues made by the lost wax method are usually hollow and can effectively control the weight, especially in the production of pieces that are head-heavy and heavily off-centered from the support point, which can be solved by making the top as thin as possible
Block Fan Method
The block fan method is the main casting method before the Shang Dynasty, it involves dividing a mold made of clay into several pieces, then pouring molten bronze into the mold, and after cooling, the mold is disassembled and the bronze casting is removed, then trimmed and polished. This method is suitable for making simple shaped bronze objects, but not for making complex shaped statues.
Separate casting method
Separate casting method is the casting method adopted since the Shang Dynasty, which is to cast the body and accessories separately and then combine them together. This method in the Shang Dynasty has been very mature, according to the need to produce a variety of complex shapes and decorations.
Modern Production Methods
The production methods of modern bronze statues have been greatly developed on the basis of traditional craftsmanship, which are mainly reflected in the following aspects:
- Precision Casting Technology: Modern bronze statues are widely produced using precision casting technology, which can produce more delicate and complex shapes through the use of precision machinery and advanced equipment.
- Improvement of lost wax method: modern lost wax method has been improved on the basis of traditional lost wax method, adopting more advanced materials and techniques, which makes the castings of higher quality, smoother surface and richer details.
- Investment casting: Investment casting is a modern method of making bronze statues, which uses wax or resin molds as inner molds to make precise castings. This method is especially suitable for making bronze statues with high precision and complex shapes.
- Computer-aided design and manufacturing: computer-aided design and manufacturing techniques are increasingly used in modern bronze statue making, and more precise and complex shapes can be produced through 3D scanning, 3D printing and other technologies.
Types of Bronze
Bronze is an alloy that consists of copper and tin along with other elements. It is usually composed of 80-90% copper and 10-20% tin . Based on the different alloy compositions and properties, bronze can be categorized as follows:
Tin Bronze
Tin bronze is the most common type of bronze and consists of copper and tin. The tin content usually ranges from 5% to 30%, and different proportions of tin bronze have different properties. Tin bronze has good mechanical properties, corrosion resistance and abrasion resistance, making it the main material used to make bronze statues.
Aluminum Bronze
Aluminum bronze is also an important type of bronze which consists of copper and aluminum. Aluminum bronze has good casting properties, and when the aluminum content is less than 7.4%, all aluminum bronze alloys are a single alpha-phase solid solution in the solid state, with good alloy plasticity and excellent machinability.
Lead Bronze
Lead bronze is a basic alloy composition of Pb, Zn, and Sn, generally with a lead content of 8% or more. The composition of Pb in bronze enhances the fatigue strength, thermal conductivity and wear resistance of the body, as well as in the working conditions with impact loads also have good performance.
Specialty Bronze
Specialty bronze, also known as high copper alloy, is a type of bronze that contains no or very little tin. This type of bronze usually contains elements such as nickel, iron, and manganese, and has special properties such as high strength and high wear resistance.
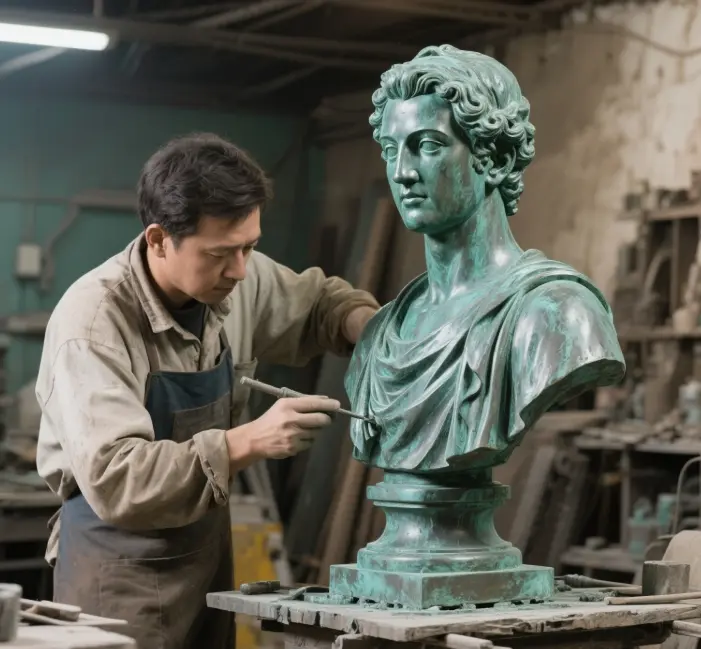
Famous Bronze Sculptors and Works
Auguste Rodin
Auguste Rodin (1840 – 1917) was a famous French sculptor whose masterpiece The Age of Bronze was created in 1877. It is a sculpture made of bronze, 180.5 centimeters high, 68.5 centimeters wide and 54.5 centimeters deep, and is now in the Musée d’Orsay in Paris, France.
The Age of Bronze is a realistic portrayal of a well-proportioned and perfectly formed young male human body, reflecting precise anatomical knowledge. The figure’s physique, facial expression, and muscle lines are so natural and vivid that it seems as if a real person is standing there. Rodin used the title “Bronze Age” to symbolize “the first awakening of mankind” and “freedom from ignorance”. The young man represented in the sculpture stands there trembling, as if he has not yet fully awakened from his slumber, but has already begun to emit inner strength, full of desire for life, emotion and vitality.
Rodin in the creation of the sculpture through the sculpture of the surface of the height of the ups and downs of the object in the fluctuation of light and shadow of the treatment of hidden, so that the sculpture has a unique vitality and artistic influence. This work was initially named “The Conquered” (or translated as “The Defeated”), which was later considered too realistic when it was exhibited in Brussels, and Rodin was even criticized as a dirty liar. When Rodin exhibited the work again in Paris, he was again ridiculed and slandered. Rodin’s teacher, Lecoq, organized a group of famous art celebrities to defend Rodin, and prompted the government to form a jury to watch Rodin sculpt in public. The jury was amazed by Rodin’s skill and eventually proved his innocence. The work was later renamed Age of Bronze and acquired by the Luxembourg Museum (now in the Musée d’Orsay).
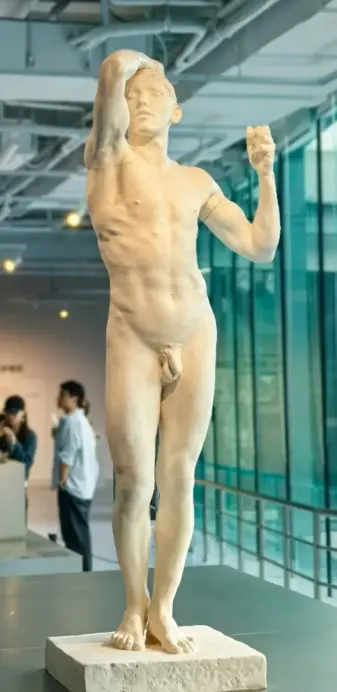
Ancient Greek bronze statue production
Ancient Greek bronze statue production technology is very exquisite, modern scholars have done a very in-depth study of large-scale bronze statues made in Ancient Greece, and found that the production method used is the lost wax casting process. This is in sharp contrast to the combined pottery casting process that was widely used in the Chinese Bronze Age.
The process of making bronze statues in Ancient Greece was roughly as follows:
First, the sculptor made an equal-sized clay model of the statue.
First, the sculptor made an equal-sized clay model for the statue. Then, a clay master mold was made around this model and split into several parts.
After the master mold dries, wax is applied to the surface of the model in an even layer to form a wax mold.
Next, a shell, usually made of clay or plaster, is made over the surface of the wax mold.
When the shell is completely dry, heat is applied to melt the wax out, creating a cavity.
Finally, molten bronze was poured into this cavity, cooled, removed, and polished and finished to give the bronze statue.
Bronze statue making in Ancient Greece pays special attention to the details of the carving and the expression of the character’s expression, through the unique texture and luster of the bronze material, the statue has a unique artistic charm. In Ancient Greece, the metal would be ground and polished, and then a varnish would be applied to the slightly yellow surface of the bronze to obtain the desired appearance.
Bronze statues in Ancient Greece were mostly characterized by figures, including mythological figures, historical figures and ordinary people. These statues not only have high artistic value, but also reflect the religious beliefs, political system and cultural traditions of ancient Greek society. Ancient Greek bronze statue production technology has had a profound impact on later generations, many modern sculptors still use the lost wax method to produce bronze statues.
Tallest Bronze Statue
India’s Statue of Unity
The tallest bronze statue in the world is India’s Statue of Unity, a 182-meter-high statue located in the western Indian state of Gujarat, which cost Rs. 29.9 billion (about $430 million). The statue is dedicated to the memory of Sardar Vallabhbhai Patel, India’s founding father.
“Construction of the Statue of Unity began in India on October 31, 2013 and is designed to be over 180 meters high. The statue used 18,000 tons of steel and 1,700 tons of bronze and was built by Larsen & Toubro. According to Indian Prime Minister Narendra Modi, the Statue of Unity is expected to become a major tourist attraction in the region.
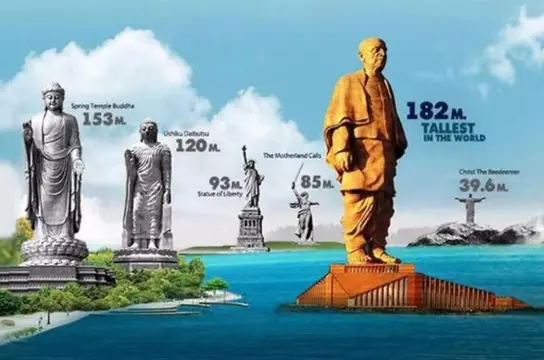
The Great Buddha of Lingshan, China
The Great Buddha of Lingshan, China is one of the tallest bronze statues in the world, standing 88 meters tall in Lingshan, China, made entirely of bronze and weighing about 700 tons. The Lingshan Giant Buddha is a symbol of Buddhist culture and an outstanding representative of Chinese architecture and casting techniques.

Reasons why bronze is used for statues
Bronze is widely used for making statues mainly because of its unique physical and chemical properties, as well as its advantages in artistic expression.
Durability
Bronze has excellent resistance to oxidation and corrosion, and can be preserved for a long time without losing its original luster and shape. Even in humid environments, bronze does not corrode as quickly as other metals, which allows bronze statues to be preserved for hundreds or even thousands of years. For example, bronze statues made during the Middle, New, and Late Kingdoms (1986-323 BC) of ancient Egypt are still well preserved today.
Expressive
Bronze has excellent malleability and casting properties, allowing a wide range of complex shapes and fine details to be produced by casting techniques. The luster and texture of bronze is also ideal for representing the skin, clothing and other details of a figure, making the statue more vivid and realistic. As stated in Bronze and Cast Bronze Sculpture, “From the casting process in terms of cast bronze sculpture process has a long history, the lost wax method of casting process is mature, the production of the sculpture for the hollow, can effectively control the weight, especially the production of head-heavy and the center of the serious deviation from the support point of the work, can be done by the top as thin as possible,… “.
Artistic Value
Bronze has a unique aesthetic value, its antique bronze luster and texture giving statues an ancient, mystical beauty. This property of bronze makes it an ideal material for making statues of historical figures, mythological figures and other statues of historical and cultural significance.
Technical Feasibility
Bronze is relatively well established for casting and can be produced in a variety of intricate shapes and details through techniques such as the lost wax method. In addition, bronze has a relatively low melting point and is easy to cast and work with, making it an ideal material for statuary.
Cultural Symbols
In many cultures, bronze is seen as a symbol of nobility, power and wealth. For example, in China, bronze was a symbol of the rights and interests of rulers in slave societies, and a reflection of the wisdom of slaves. Therefore, making statues from bronze not only has artistic value, but also has cultural symbolism.