As an important artwork and monument, bronze statues have played a pivotal role in the history of human civilization. From ancient bronzes to modern bronze statues of human figures, the production process of bronze statues has evolved over thousands of years. This presentation will explore in detail the process of making bronze statues, including the traditional lost-wax method and modern bronze casting techniques, with special attention to key steps such as clay carving, rubber molding, wax removal, casting, casting and removal of ceramic shells, finishing processes, and how large-scale bronze statues are made.
Traditional Bronze Statue Making Method
Fan casting method
Fan casting method is the main bronze casting method used in ancient China, and its process mainly includes four steps: group model, casting, cooling and polishing. Casting bronze knights, for example, the first yellow clay to make a model of the object, that is, “mold”. In the mold of the surface covered with mud, to be solidified and then peeled down in areas to form the outer model. At the same time in the mold cavity filled with clay, the formation of the inner model, or the mold scraped off a certain thickness to form the inner model. The beautiful patterns on the bronzes are engraved on the inside of the outer mold. The inner fan and outer fan are combined together to form a cavity between the two, and then the smelted copper liquid is poured into it from the pouring mouth, and after cooling and drying, the outer fan and inner fan are broken, trimmed and polished, and a fine bronze vessel is cast.
Lost-wax method
The process of lost-wax method includes: wrapping the clay embryo, pouring fine clay, covering thick clay; melting wax in the kiln; and forming a cavity. Firstly, easy-to-melt materials (e.g. beeswax, animal oil, etc.) are selected to make wax blocks, which are then carved into the objects to be cast, i.e. wax molds. After that, the surface of the wax mold is drenched with fine mud, then covered with thick mud on the outer surface, dried in the shade and baked so that the wax mold melts and flows out to form a cavity, i.e. lost wax. Finally, the cavity was filled with copper liquid, cooled and polished to obtain the bronze ware. With the invention of the lost wax method, it is possible to cast almost any style of bronze, including those extremely elaborate masterpieces that amaze modern people!
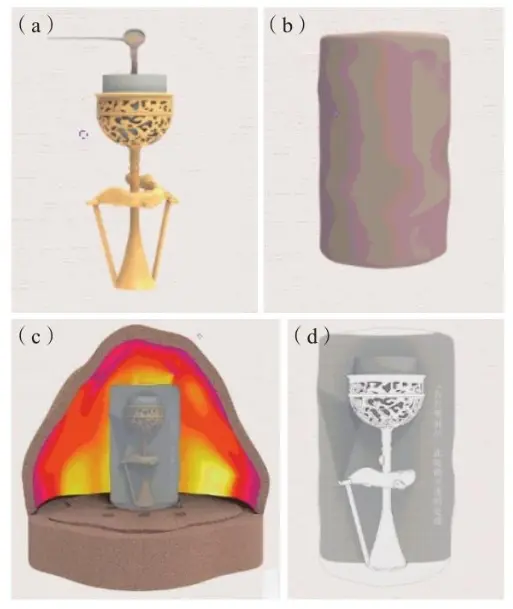
Modern Bronze Statue Making Method
Clay Sculpture and Design
The first step in modern bronze statue making is clay sculpture and design. The first step is to design a drawing for the overall conception of the sculpture, and then cast the bronze sculpture according to the design. Then use the clay draft to make a generalized model, which is convenient for us to complete the design, and if there is anything bad, we can change it on the clay sculpture. Then the design of the design, using the clay manuscript to make a generic model to facilitate us to complete the design, if there is anything bad, we can change the clay sculpture.
In modern crafts, one-to-one clay modeling is usually done first. Design program deepening and clay production is the first step of the entire production process, first of all, the overall concept of the sculpture and design drawings, and then in accordance with the pattern of the appearance of the casting of the bronze sculpture, and then it is the design of the pattern with the clay to make a rough model out, to facilitate us to finalize the model, if there is anything bad we can change in the clay, in the second is to enlarge the clay according to the proportion of the clay, for a one-to-one The next step is to enlarge the clay model to scale and make a one-to-one clay model.
Mold Turning
After the clay sculpture is finished, it is necessary to turn the mold. There are generally two types of molds: one for plaster and one for silicone. Plaster turning is used in less complex cases and vice versa with silicone. Choosing the appropriate mold turning material according to different needs and complexity is the key to ensure the smoothness of the subsequent production process.
Wax mold filling
The melted paraffin wax is filled into the already made plaster molds or silicone molds, and when the paraffin wax cools down, it becomes a wax mold. This process requires precise control of temperature and time to ensure that the quality of the wax pattern meets the requirements.
Shell making and casting
There are two types of shell making and mold turning alike: one is precision casting and the other is resin sand box making. In small or complex pieces, precision casting should be chosen, while sandbox making is generally suitable for simple glossy surfaces without much craftsmanship.
Copper is melted into copper water under high temperature environment and poured inside the well-made shell or sand box, and then the riser is cleared and polished. This process requires strict control of the temperature and fluidity of the copper water to ensure the quality of the bronze statue.
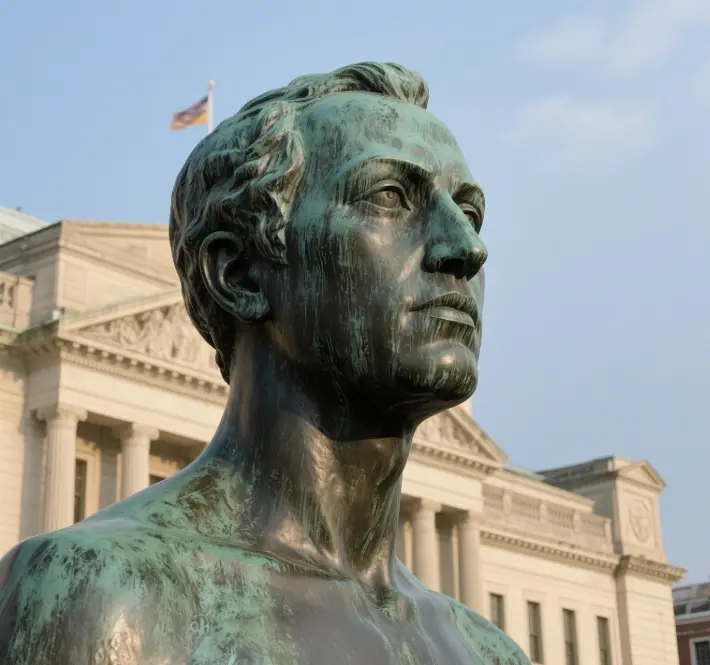
Special production process of large bronze statues
For the production of very large and complex bronzes, the method of split casting and jointing is usually used. For example, a large bronze mask consists of multiple parts such as the face, the back of the cheeks, the eyes, and the ears, which are cast separately and then combined into a single piece.
In modern times, for extra-large statues such as the 58-meter-high bronze statue of Guan Gong in Jingzhou, advanced release techniques are used. The release of the finalized model of the bronze statue of Guan Gong was mainly carried out using a handheld laser 3D scanner, and the EPS foam was processed according to a 1:1 model using a high-end CNC three-axis machining machine. The texture is refined with plaster on the surface of the foam mold. One horizontal layering every 2 meters, assembled layer by layer. Every two layers for upper and lower positioning, creating a new model of large-scale sculpture placement.
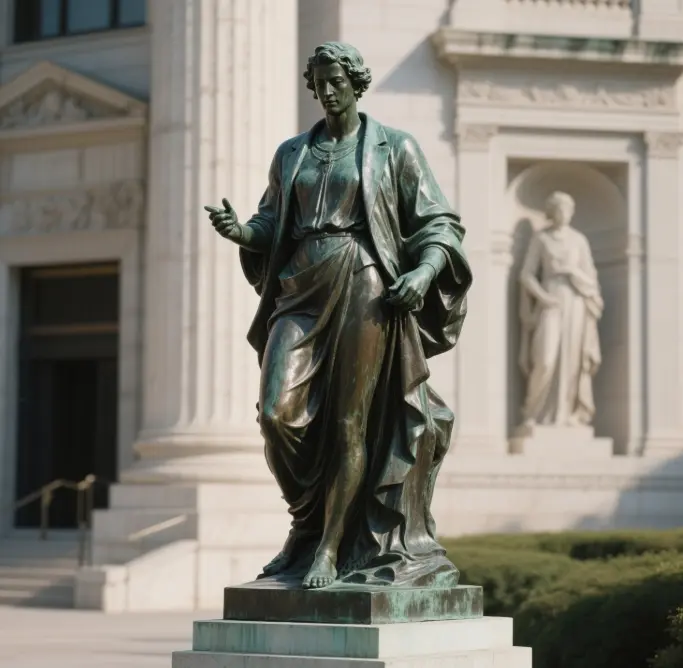
Finishing Process
Sanding and Polishing
Finishing is the last process of bronze processing, which includes sanding, color plating, engraving and other steps. Polishing can make the surface of bronze products smoother and more glossy; color plating can add color to the bronze products and make them more beautiful.
In modern bronze statue production, finishing includes the following steps: put together the bronze sculpture that has been polished to become a complete whole, then clean up the welded joints and the surface for coloring, followed by oiling and sealing wax, so that the sculpture will remain up-to-date for a long time.
Chemical polishing techniques
Copper polishing is done by the common methods of physical polishing, chemical polishing, electrolytic polishing, and some newer methods including ultrasonic polishing and fluid polishing. Currently in the copper industry, the application of chemical polishing is gradually becoming mainstream, because this process can solve the problem of copper not shining. Copper chemical polishing is the use of copper chemical polishing brightener to eliminate the unevenness of the copper surface and enhance the brightness of the copper surface through chemical action.
When building the bath, the polishing agent and water are diluted according to 1:2~3 to water to be used. The equipment requirement is a plastic container as the polishing bath, and it is recommended to use PVC or PP type material to make the bath. If the production volume is large, the tank body needs to do constant temperature (cooling) design, to ensure that the solution temperature is stable and uniform during the production process. The method of use is to configure the polishing solution heated to 40 ~ 50 ℃, put the cleaned copper parts in the polishing solution immersed in about 1 ~ 3 minutes after removing, washed with water. At this time, the surface of the copper has formed a brown translucent oxide film. Then put the copper parts into the depolishing solution immersed in about 3-8 seconds can be the surface of the brownish-yellow film back to the net and show a bright surface.
The process flow is as follows: degreasing and degreasing – rinsing – chemical polishing of copper – rinsing – film removal – rinsing – passivation of copper – rinsing rinsing – pure water rinsing – drying – finished product packaging.
Gilding process
In the production process of copper Buddha statue, gilt Buddha statue is one of them. Modern copper Buddha statue if we talk about craftsmanship, we have to count the gilt Buddha statue! In the production process of copper Buddha statues, gilt Buddha statues are absolutely second to none, and modern copper Buddha statues are mostly made with gilt-treated surfaces, which shows the wide application of gilt Buddha statues.
Gilding is an ancient Chinese metal decorative craft, in which gold is firmly attached by applying gold-mercury amalgam (gold clay) to the surface of a bronze vessel and heating to evaporate the mercury . This process is not only aesthetically pleasing, but also effectively protects bronze statues from oxidation.
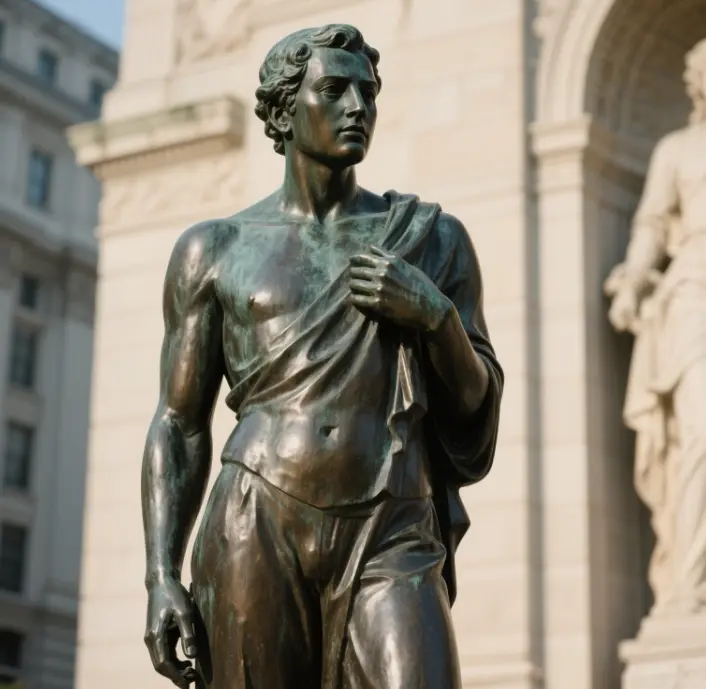
Hollow Bronze Casting
Hollow bronze casting is a special casting technology, mainly used for making large bronze statues or decorations. Compared with solid casting, hollow casting has the advantages of light weight, saving material and reducing casting difficulty.
In hollow bronze casting, the first need to make the inner core. Clay as the main component, add the right amount of fine sand and organic material (horse manure, pulp) made of clay core. Part of the clay core is added with iron wire as the core bone to increase the strength of the clay core.
Wax molds were then made. The wax material consists of wax, rosin and grease, and the ratio of wax mold materials varies depending on the object. For high strength, rosin-based waxes are used; for good plasticity, beeswax-based waxes are used. Since the plasticity of wax is related to the climate change, the amount of oil added is used to adjust it. After melting wax and rosin, add grease, mix well, and condense to become wax material. Wax molds are made by wax stripping method or wax dialing method.
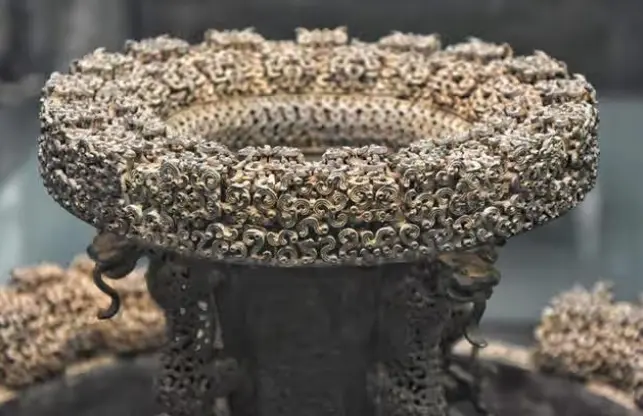
Production of Large Bronze Statues
Design and Production Process
The production process of large bronze statues usually includes the following steps: deepening the design scheme and clay modeling, mold turning, wax molding, shell making, casting and polishing, splicing and forming, cleaning the welds and surface coloring, oiling and sealing, as well as installation.
For the production of very large and complex bronzes, the method of casting and joining is usually used. For example, a large bronze mask consists of the face, the back of the cheeks, eyes, ears and other parts of the casting, and then combined into one.
Installation and Maintenance
After the production of large bronze statues is completed, the last step is installation. When installing, it usually requires professional personnel to guide the installation according to the site construction environment.
In order to ensure that the bronze statue can be preserved for a long time, regular maintenance is required. Maintenance includes cleaning the surface, checking the structural stability, and repairing when necessary. These maintenance tasks can effectively extend the service life of the bronze statue and maintain its beauty and historical value.
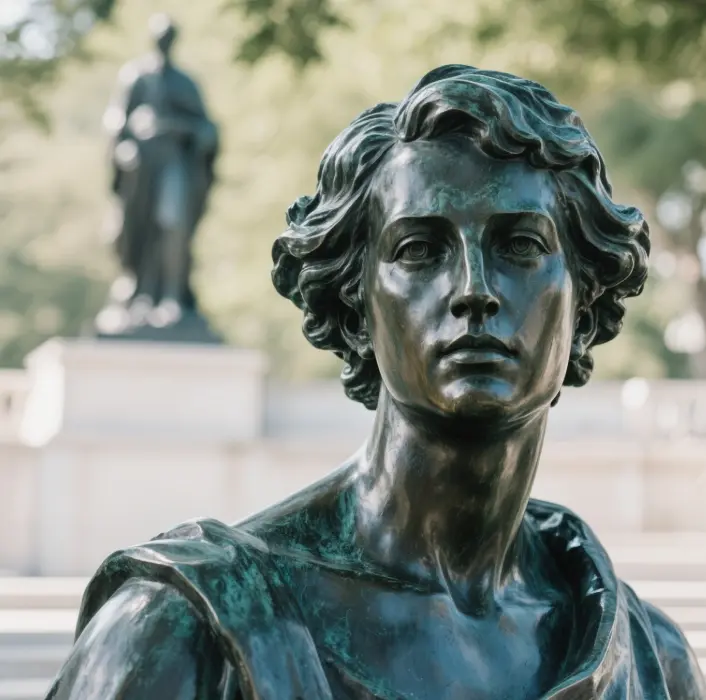
Modern Technology Application of Bronze Statue Production-3D Printing Technology
The application of 3D printing technology is becoming more and more widespread in modern bronze statue production. By obtaining model data through 3D scanning, every detail of the original statue can be accurately replicated to ensure that the replica is highly consistent with the original. For example, the square circle sculpture “Son of the Earth” is 4.3 meters high and 9 meters wide, Prof. Dong Shubing, through combing and researching the large-scale sculptures in the world, and trying to apply the materials available for the creation of large-scale sculptures in the country, chose red sandstone as the main material, and used 3D scanning to obtain the model data.
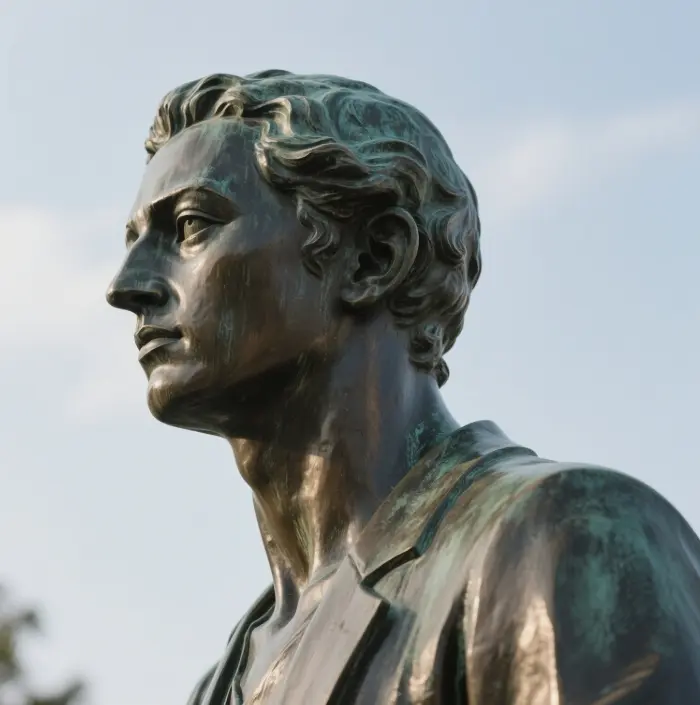
The process of bronze statue making has evolved and developed over thousands of years, from the ancient lost wax method to modern digital design and production. Both the traditional lost wax method and the modern digital technology reflect the human wisdom and craftsmanship. Modern bronze statue production integrates the use of traditional craftsmanship and modern technology, making the production of bronze statues more precise and efficient, while retaining the essence of traditional craftsmanship.
In the production of large bronze statues, the application of technologies such as split-casting and jointing, mold turning, etc. makes the production more flexible and efficient. Finishing processes such as grinding, polishing and gilding make the surface of bronze statues smoother and more beautiful, with higher artistic and ornamental value.
With the development of science and technology, the application of modern technology such as 3D printing and computer-aided design will further promote the development of the bronze statue production process, making the production of bronze statues more accurate and efficient, and at the same time creating more bronze statues with the characteristics of the times.